O cimento está, discretamente, em todo o lado no nosso dia a dia: é utilizado na construção de estradas, edifícios, barragens e infraestruturas subterrâneas. No entanto, existe uma ameaça climática oculta entre estes blocos cinzentos omnipresentes. A produção de cimento representa mais de 7% das emissões globais de dióxido de carbono, superando setores como a aviação, o transporte marítimo e os aterros sanitários.
Os seres humanos produzem cimento, em diferentes composições, há milhares de anos. Os antigos romanos utilizavam cinzas vulcânicas, cal triturada e água do mar para construir aquedutos e monumentos icónicos como o Panteão. A versão moderna do cimento hidráulico (o tipo que endurece ao secar quando misturado com água) é utilizada desde o início do século XIX. Derivado de materiais amplamente disponíveis na natureza, é um produto barato e fácil de fabricar. Atualmente, o cimento é um dos materiais mais utilizados no planeta, com cerca de quatro mil milhões de toneladas produzidas anualmente.
O cimento produzido em escala industrial representa um dilema climático para muitos setores. A sua produção consome enormes quantidades de energia: o interior de um forno tradicional de cimento atinge temperaturas superiores às da lava de um vulcão em erupção. Para alcançar esses níveis de calor, é frequentemente necessária a queima de combustíveis fósseis, como carvão. Além disso, as reações químicas envolvidas na transformação de minerais triturados em cimento libertam dióxido de carbono, o gás de efeito de estufa mais comum na atmosfera.
Uma solução para este problema climático pode estar a ser desenvolvida pela Sublime Systems. Fundada por dois cientistas do MIT especializados em tecnologia de baterias, a startup está a desenvolver um método inovador de produção de cimento.
Em vez de aquecer rochas trituradas em fornos a altas temperaturas, a Sublime submerge os materiais em água e aplica descargas elétricas, desencadeando reações químicas que resultam nos principais componentes do cimento sintetizado pela empresa.
Nos últimos anos, a startup passou de uma produção experimental limitada para a construção de uma fábrica-piloto, com capacidade para produzir cerca de 100 toneladas de cimento por ano. Embora esta quantidade seja insignificante em comparação com as fábricas tradicionais, que podem produzir mais de um milhão de toneladas anualmente, a instalação representa um primeiro passo crucial para demonstrar que a eletroquímica pode ser uma alternativa viável na produção de um dos materiais de construção mais importantes do mundo.
Até ao final da década, a Sublime planeia operar uma fábrica de grande escala, capaz de produzir um milhão de toneladas de cimento por ano. No entanto, construir e equipar fábricas tradicionais de cimento pode custar mais de mil milhões de dólares. Competir com empresas consolidadas no setor exigirá um crescimento acelerado da startup e a captação de financiamento substancial para suportar essa expansão.
O fim das taxas de juro próximas de 0% torna esta tarefa ainda mais desafiadora, especialmente para uma empresa que fabrica uma matéria-prima como o cimento. Além disso, num setor de elevado risco e margens reduzidas, a Sublime precisará de convencer as construtoras a adotarem o seu material em detrimento dos produtos concorrentes.
A indústria cimenteira emite 2,6 mil bilhões de toneladas de dióxido de carbono por ano. Resolver este problema exige enfrentar duas fontes distintas de emissões de gases de efeito de estufa: o calor necessário para a produção e as reações químicas inerentes ao processo.
Atualmente, a produção de cimento envolve a trituração e aquecimento de uma mistura que geralmente contém calcário, areia e argila, em fornos que atingem temperaturas de até 1.500°C. O calor desencadeia reações químicas que transformam o calcário em cal e combinam-no com o dióxido de silício presente na areia e na argila. Embora o processo seja complexo, o produto final essencial consiste numa combinação de compostos de silício, cálcio e oxigénio, que permitem que o cimento endureça quando misturado com água, areia e brita, formando o betão, um dos materiais de construção mais resistentes.
Depois da água, o betão é o material mais utilizado no mundo, sendo o cimento o elemento que o mantém coeso, representando cerca de 10% do seu volume. Aproximadamente 40% das emissões de gases de efeito de estufa associadas à produção de cimento resultam da queima de combustíveis fósseis para gerar calor. Este é um problema comum na indústria pesada, onde os combustíveis fósseis tornaram-se essenciais devido ao seu baixo custo, explica Rebecca Dell, responsável pela área industrial no grupo de investigação sem fins lucrativos ClimateWorks. No entanto, com a crescente adoção de energias renováveis no setor elétrico, abrem-se oportunidades para que mais indústrias passem a utilizar eletricidade nos seus processos produtivos.
A utilização de fornos elétricos para a produção de cimento é uma possibilidade e algumas das principais empresas do setor, como a Cemex, já estão a explorar essa tecnologia para reduzir as emissões associadas à geração de calor. Se alimentados por eletricidade renovável, estes fornos poderiam representar uma solução promissora para mitigar os impactos climáticos da indústria cimenteira.
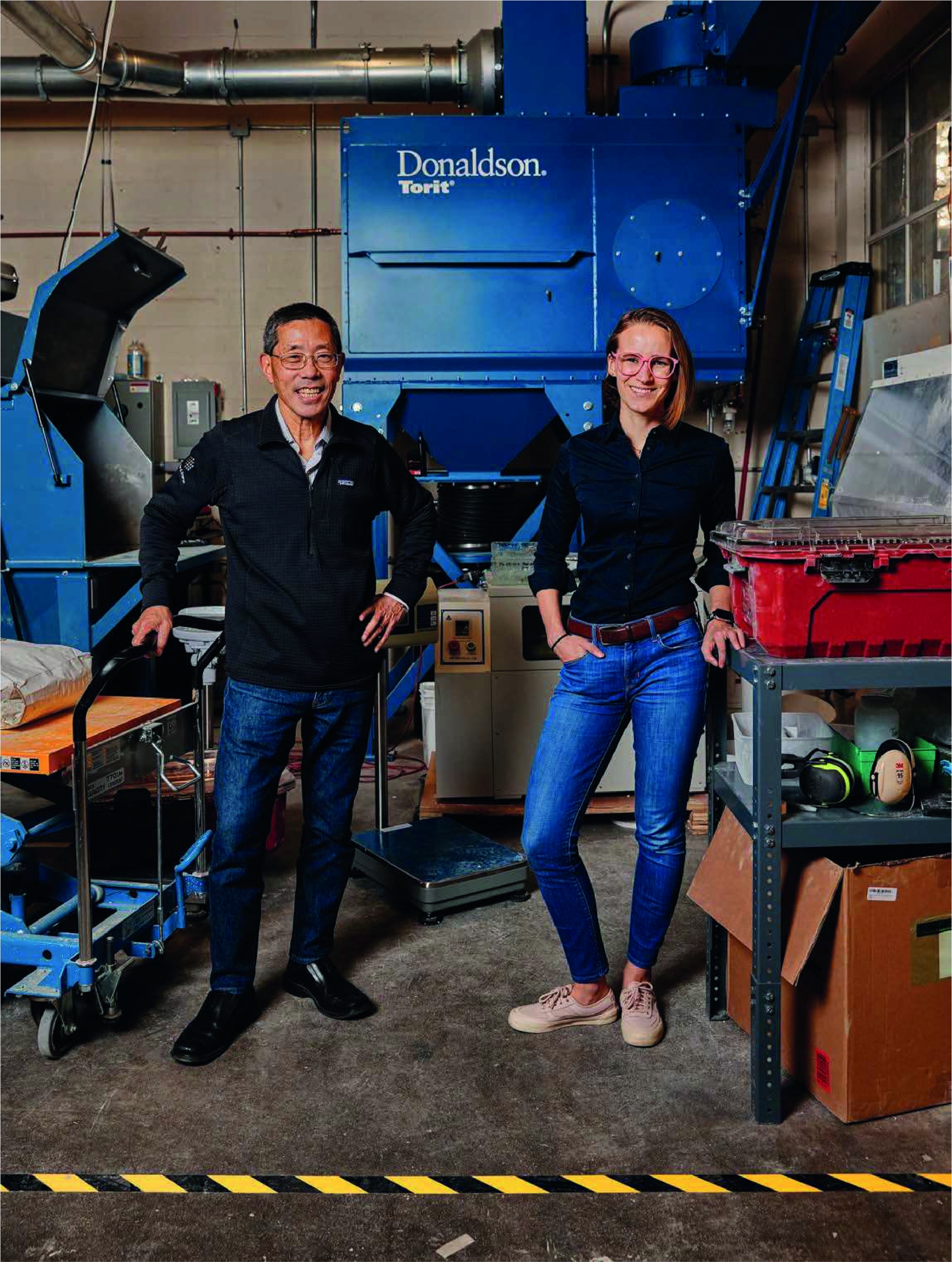
Contudo, essa abordagem não resolve o problema das emissões provenientes das reações químicas envolvidas na produção de cimento, que representam cerca de 60% do total. A maioria dos cimentos tem como base o calcário, uma rocha sedimentar composta por cálcio, oxigénio e carbono. Durante o processo de fabrico, o calcário é decomposto em cal e dióxido de carbono, libertando grandes quantidades deste gás para a atmosfera. Estas emissões podem ser significativas e acumulam-se rapidamente na atmosfera, contribuindo para o aquecimento global. Assim, a descarbonização total da indústria do cimento poderá exigir uma transformação mais radical.
É aqui que entra a Sublime. “O cimento não recebe o reconhecimento que merece”, afirma Leah Ellis, cofundadora e CEO da empresa.
Ellis não planeava ingressar na indústria dos materiais de construção. Cresceu no Canadá e realizou os seus estudos de pós-graduação sob a orientação de Jeff Dahn, um pioneiro na tecnologia de baterias. Mais tarde, ingressou no MIT para trabalhar com Yet-Ming Chiang, um empreendedor versátil e referência na investigação de baterias. Chiang fundou diversas empresas de armazenamento de energia, como a A123 Systems, a 24M e a Form Energy, e é agora cofundador da Sublime Systems.
Quando Ellis chegou ao MIT, Chiang sugeriu-lhe que explorasse um tópico diferente para as suas investigações. Perguntou-lhe se já estava cansada de estudar baterias. “Pensei que fosse uma pergunta armadilhada”, lembra Ellis, “porque ele é, obviamente, um cientista de baterias de renome”. No entanto, Chiang tinha a ideia de produzir cimento de uma nova forma, utilizando a eletroquímica — uma abordagem comum na ciência das baterias.
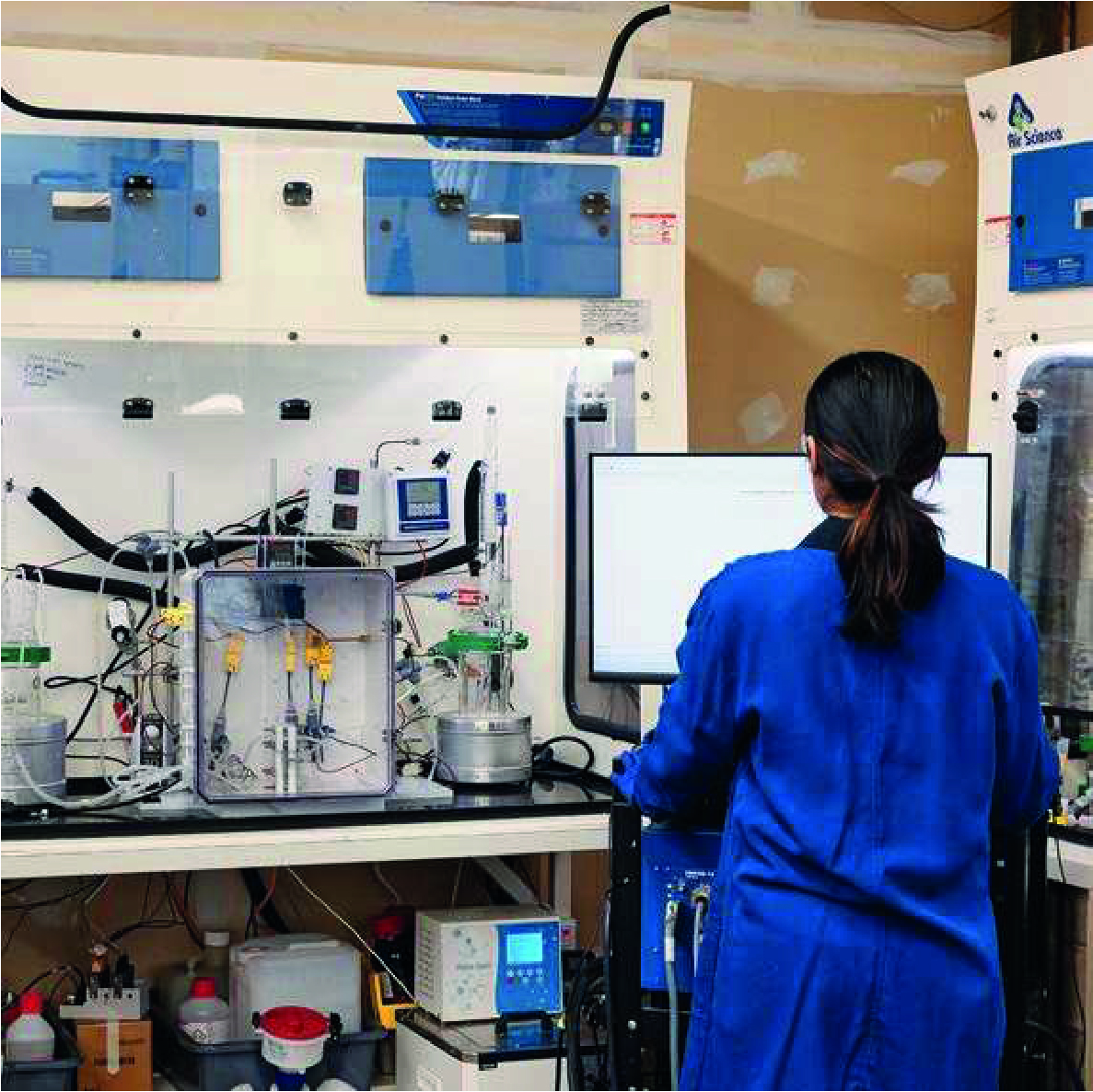
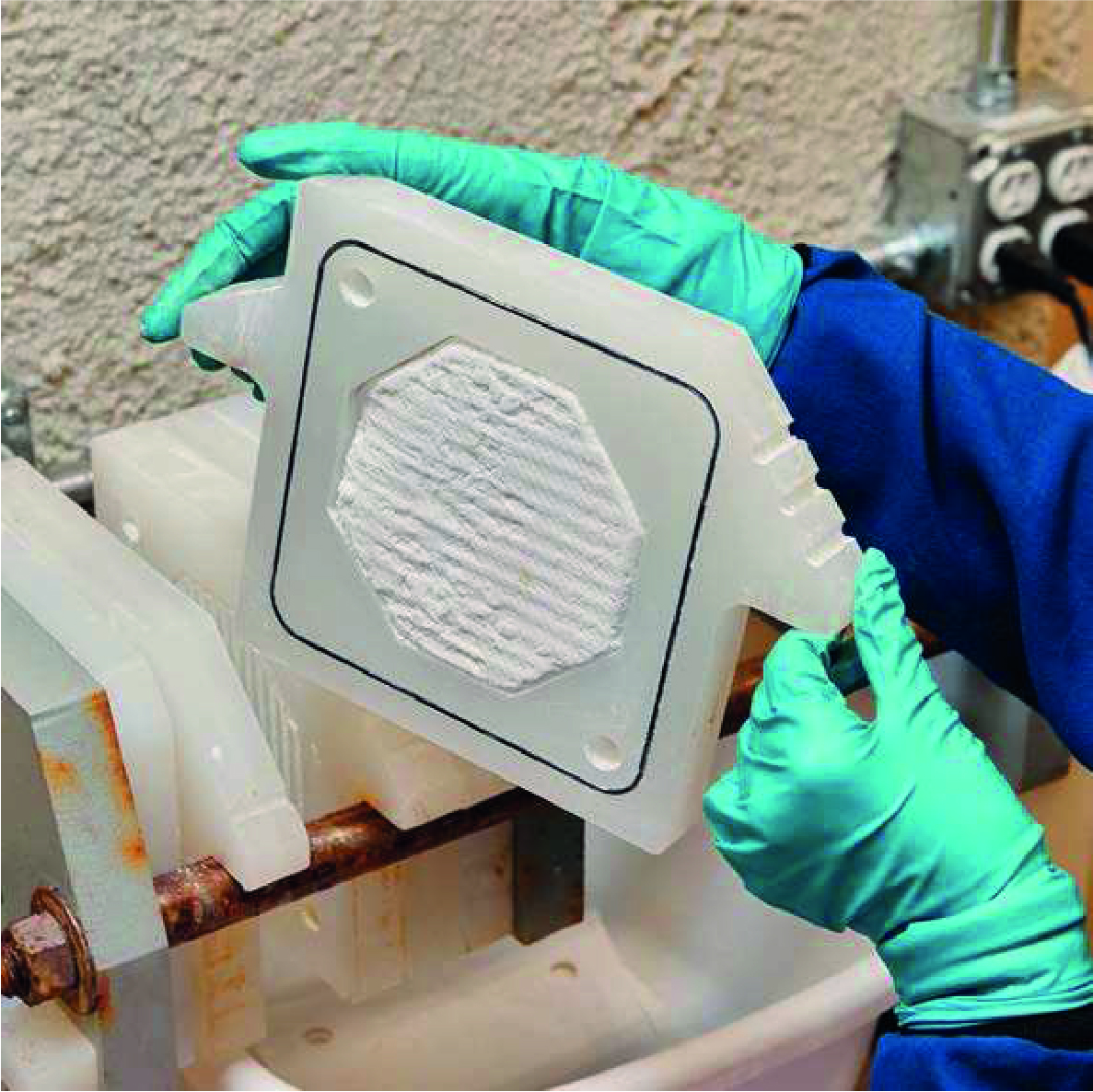
Em 2019, Ellis e a sua equipa descobriram um método promissor para concretizar essa visão. Usando um eletrólito, conseguiram criar variações graduais de pH num tanque, dissolvendo calcário numa extremidade e formando cal hidratada na outra. Essa cal poderia então ser combinada com sílica reativa para produzir os mesmos compostos presentes no cimento tradicional.
Após uma análise de mercado e um aprofundamento técnico, Ellis e Chiang decidiram fundar a Sublime, com Ellis à frente da empresa. Hoje, a startup opera uma linha de produção em pequena escala, testando e otimizando os seus processos de fabrico. É um progresso significativo desde os primeiros dias no MIT, quando a equipa produzia apenas pequenas quantidades de material — o suficiente para fabricar um simples dado de cimento. Segundo Mike Corbett, diretor de engenharia da Sublime, a nova linha de produção, lançada no final de 2022, é 20 vezes maior do que qualquer experiência anterior realizada em laboratório.
Operando na sua capacidade máxima, a linha de produção experimental da Sublime levaria uma semana para produzir cimento suficiente para abastecer um único camião betoneira.
Numa sala espaçosa na sede da startup, os tanques de aço inoxidável estão dispostos ao longo das paredes de forma mais ou menos ordenada, da esquerda para a direita. Nos tanques de um lado da sala, são depositadas rochas trituradas e, nos outros, é produzida cal hidratada, um dos principais ingredientes do cimento da Sublime. Os resultados de vários experimentos e testes de investigação e desenvolvimento ficam ao lado, em baldes de quase 20 litros empilhados em suportes metálicos. Quando Corbett e um colega abrem a tampa de um deles, encontramos a cal hidratada no seu interior: um pó branco despretensioso, com aspeto de farinha e ligeiramente grumoso, parecendo bicarbonato de sódio deixado numa embalagem aberta há demasiado tempo. Seria difícil utilizar o que está nesses baldes para construir seja o que for: operando na sua capacidade máxima, a linha de produção experimental da Sublime levaria uma semana para produzir cimento suficiente para abastecer um único camião betoneira. E são necessários o equivalente a três a quatro camiões para betonizar a fundação de apenas uma casa para uma família nos EUA. Em vez disso, a startup produz material para enviar a potenciais parceiros, realizando testes em blocos de cimento e, sobretudo, ajudando a projetar as próximas unidades de produção em larga escala. Estas, significativamente maiores, poderão ser a última etapa para demonstrar que o processo da Sublime pode funcionar na indústria cimenteira.
A Sublime Systems não é a única empresa a tentar tornar o cimento mais ecológico. As primeiras tentativas para reduzir as emissões do cimento concentraram-se sobretudo na questão da eficiência, diz Radhika Lalit, diretora de iniciativa para a indústria na Climate Imperative Foundation, que anteriormente trabalhou no setor industrial no Rocky Mountain Institute (RMI), uma agência de investigação sem fins lucrativos. Por exemplo, a adição de materiais de enchimento, denominados materiais cimentícios suplementares, que conseguem reagir com os ingredientes ativos do cimento, pode ajudar a reduzir as emissões totais de gases sem comprometer as propriedades do betão. No entanto, esta estratégia só funciona até certo ponto, sublinha Lalit: a partir daí, esses enchimentos começam a degradar a resistência e a durabilidade do cimento. Existem outras formas de adicionar materiais ao cimento para reduzir os impactos climáticos. Por exemplo, a empresa canadiana CarbonCure Technologies desenvolveu uma técnica para injetar dióxido de carbono em misturas de cimento. Segundo a CarbonCure, o gás injetado reage com os componentes do cimento e transforma-se em minerais sólidos, incorporando assim o carbono na estrutura do betão. Isto não só reduz as emissões de carbono, como também melhora a resistência do material, tornando-se uma potencial solução para o armazenamento de carbono a longo prazo. A CarbonCure está a trabalhar com empresas especializadas na remoção destes gases da atmosfera, como a Heirloom Carbon Technologies, para explorar essa possibilidade.
Contudo, métodos que envolvem a redução total do material utilizado ou a adição de ingredientes de enchimento têm limitações quanto à redução das emissões: é impossível fazer ajustes de eficiência ilimitados para as eliminar por completo. Por isso, muitas empresas já estabelecidas no setor do cimento procuram adicionar centrais de captura e armazenamento de carbono às fábricas existentes, diz Lalit. Isto permitiria que as fábricas em funcionamento capturassem o dióxido de carbono dos gases emitidos antes de serem libertados para a atmosfera, reduzindo assim as emissões e contribuindo para tornar a indústria mais sustentável, sem a necessidade de substituir por completo as instalações. A adição de tecnologia de captura de carbono às infraestruturas já existentes poderia prolongar a vida útil dos equipamentos habitualmente utilizados na indústria pesada, um grande benefício para as fábricas construídas recentemente, que em geral são projetadas para operar entre 30 e 50 anos. No entanto, a eficácia da captura de carbono ainda não foi plenamente comprovada pelo setor: os métodos existentes muitas vezes não conseguem capturar as emissões na totalidade, e as poucas instalações em grande escala que adotaram esta tecnologia enfrentaram problemas ou dificuldades na sua implementação, afirma Lalit.
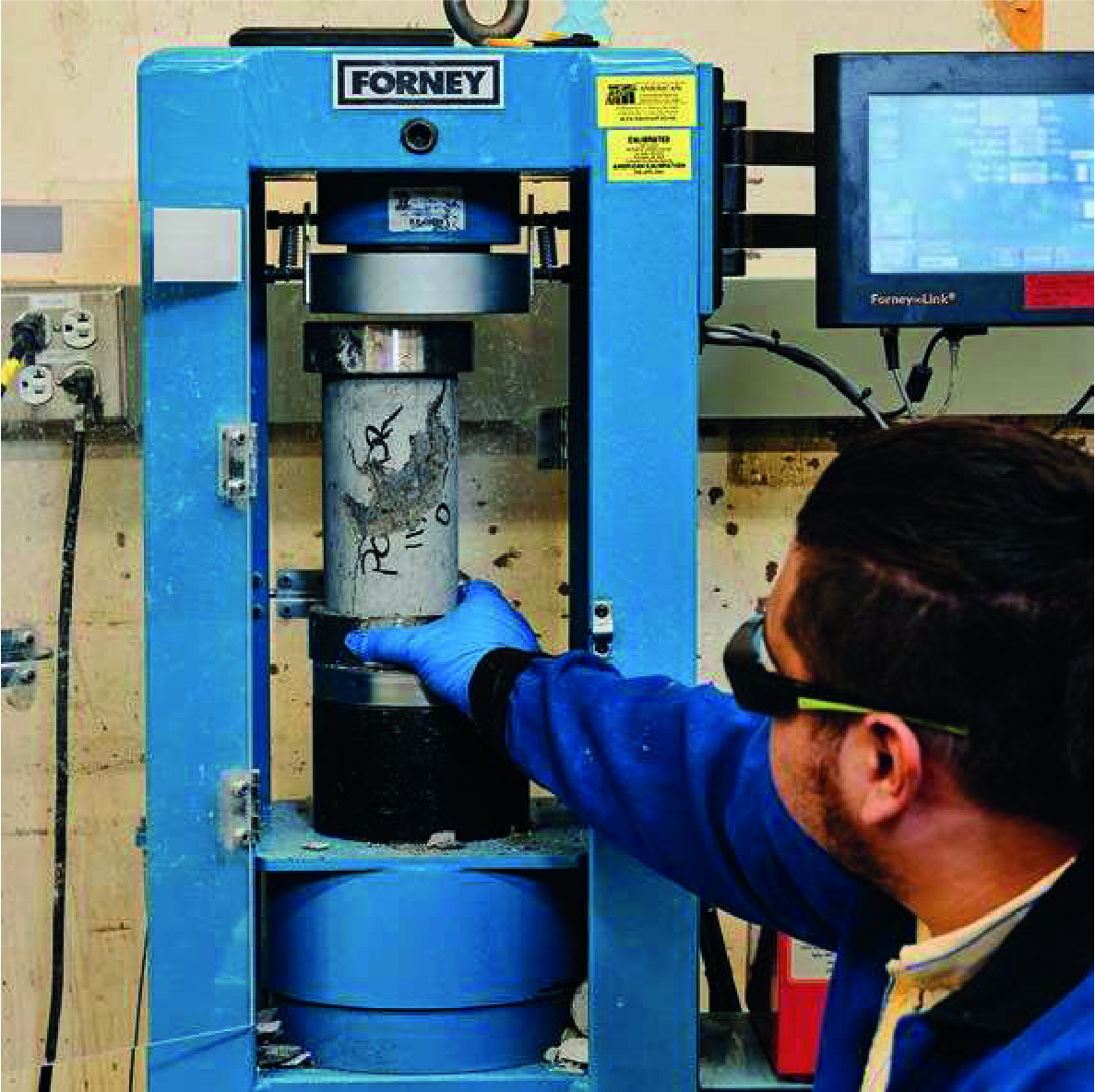
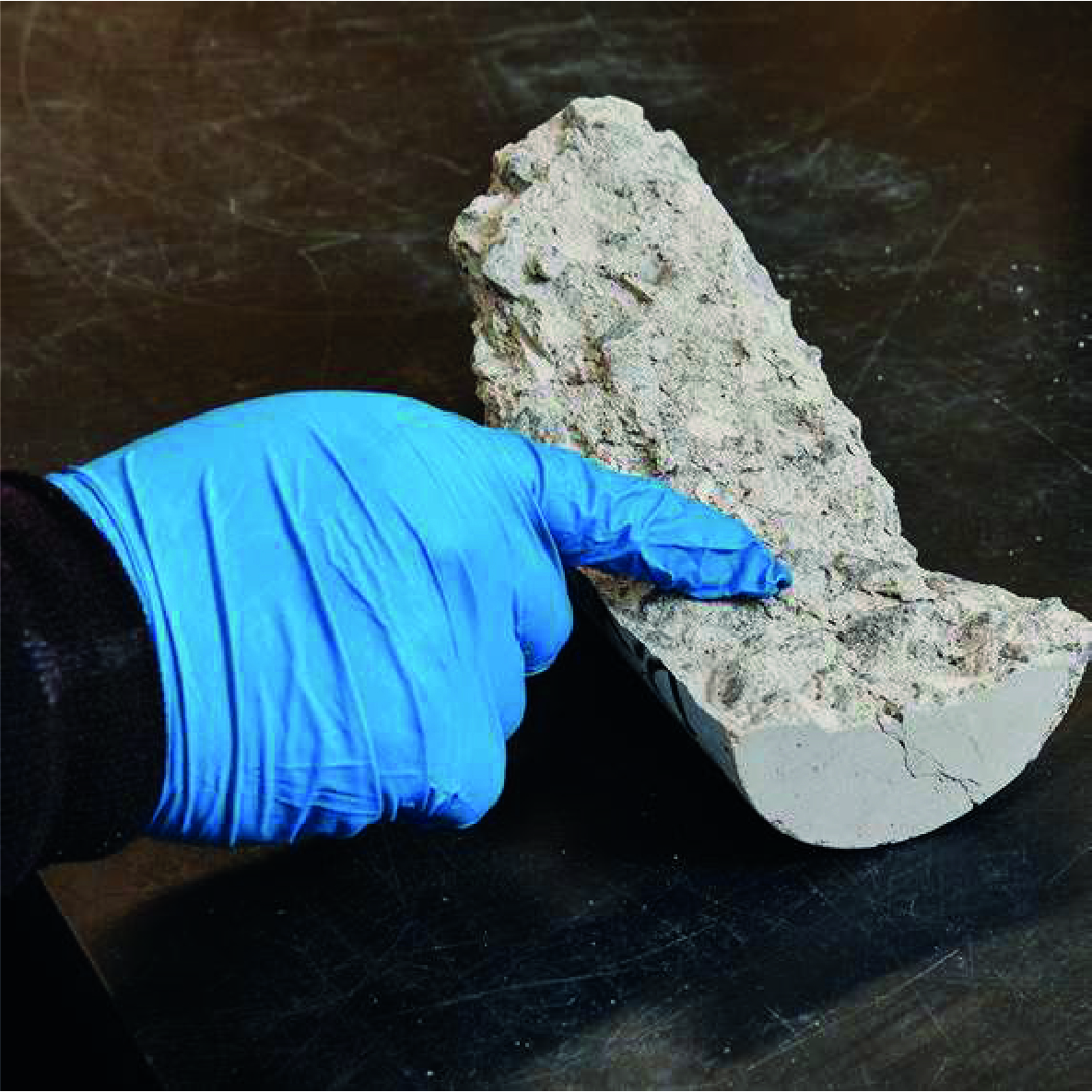
Para cumprir as metas de emissões líquidas zero, a indústria do cimento precisaria de adicionar instalações de captura de carbono em cerca de 33 a 45 fábricas já existentes até 2030, segundo o RMI. A primeira instalação industrial deste tipo numa fábrica de cimento está programada para entrar em funcionamento ainda este ano. No entanto, isto poderá ser dispendioso: um sistema de captura de carbono pode custar até 120 dólares por tonelada de dióxido de carbono removido, o que, segundo Ellis, quase duplicaria o custo final do cimento aos preços atuais. O custo é uma das razões pelas quais a Sublime e várias outras startups estão a evitar a captura de carbono, focando-se antes na redução da pegada de carbono do cimento através de métodos mais radicais.
Uma das startups de cimento com maior financiamento é a Brimstone, um grupo sediado na Califórnia (EUA) que emprega um processo que considera ser carbono-negativo na produção de cimento. “Isto significa que o produto acaba por retirar mais dióxido de carbono da atmosfera do que emite”, afirma Cody Finke, CEO da Brimstone. O processo baseia-se em duas estratégias principais. Primeiro, em vez de calcário, a Brimstone utiliza outros minerais chamados silicatos, que não contêm dióxido de carbono, eliminando assim as emissões do seu processo de fabrico de cimento, explica Finke. Além disso, um subproduto dos silicatos é um material que contém magnésio, que atua como uma esponja, absorvendo dióxido de carbono do ar e mineralizando-o.
Ainda existem emissões associadas à produção do cimento da Brimstone, sobretudo devido à energia necessária para o processo. No entanto, estas podem ser efetivamente neutralizadas pelo processo mineral, explica Finke, especialmente porque a empresa planeia utilizar fornos elétricos. Se forem alimentados pela eletricidade da rede elétrica convencional dos EUA, afirma a startup, o seu material acabaria por remover mais dióxido de carbono do que emitiria (cerca de 130 quilogramas adicionais por tonelada de cimento). A razão pela qual a Brimstone mantém este processo de alta temperatura, apesar das suas necessidades energéticas e emissões associadas, deve-se ao facto de produzir um cimento com uma fórmula química já dominante na indústria. O cimento Portland, que existe desde o início do século XIX, é provavelmente o primeiro que nos vem à mente ao pensar em cimento. Ele é conhecido por produzir um betão resistente e com padrões já estabelecidos pelo setor. No entanto, há um problema: a sua produção requer temperaturas extremamente elevadas, uma vez que um ingrediente-chave do cimento (a alita) só se forma a temperaturas superiores a 1.250°C.
Inicialmente, a Sublime também planeava produzir cimento Portland. “Para algo tão acessível quanto cimento, pensávamos que precisaríamos de fabricar aquilo a que o mercado já está habituado”, diz Chiang. Mas os requisitos de temperatura levaram a Sublime a reconsiderar essa abordagem à medida que a sua produção escalava: “estávamos a tentar inovar com uma invenção criada há mais de 200 anos”. Assim, a equipa investigou e descobriu que existem outros caminhos para criar ligações químicas que conferem resistência ao betão feito com cimento Portland. O material da Sublime segue uma dessas rotas alternativas: em vez de alita, utiliza cal e silicatos reativos, que reagem com a água para formar o material final.
A escolha da composição química do cimento pode parecer um detalhe técnico. Mas, numa indústria de elevado risco como a construção, pode ser determinante para definir quais as startups que conseguirão grandes contratos e parcerias — e quais desaparecerão. “Acho que as pessoas são, com razão, cépticas em relação a um novo cimento”, diz Ellis, antes de se corrigir: “bem, é e não é um novo cimento”. Ellis afirma que o material da Sublime é tão resistente e durável quanto o cimento Portland, se não mais. No entanto, há a possibilidade de que os profissionais do setor da construção hesitem, pelo menos inicialmente, em abandonar um material que já conhecem, diz Lalit, da Climate Imperative.
Casey Crownhart é uma repórter da MIT Technology Review focada em artigos sobre o clima.